在化工、制药、材料合成等领域,低温反应釜是进行低温化学反应、聚合反应等工艺的关键设备。其控温精度直接影响反应的安全性、产物质量和生产效率。然而,实际生产中常出现控温超差报警频发的问题,严重干扰生产流程,增加能耗和人工成本。本文从传感器和 PID 调节两个关键因素入手,深入分析问题成因并探讨解决方案。
一、传感器因素分析
传感器作为温度信号的采集元件,是控温系统的 "眼睛",其性能和状态直接决定控温精度。
(一)传感器选型不当
不同低温反应釜的工作温度范围、介质特性(如腐蚀性、粘度)和反应压力差异较大。若传感器的量程、精度、耐温性和耐腐蚀性不符合工况要求,会导致信号采集失真。例如,在 - 80℃以下的超低温环境中,普通热电偶传感器可能因材料特性变化出现较大测量误差,而未选用适合低温的铂电阻传感器(如 Pt100)。此外,传感器的响应时间过长,无法及时捕捉温度快速变化,也会使控温系统滞后,引发超差。
(二)传感器安装问题
传感器的安装位置和方式对测量准确性至关重要。若安装位置靠近加热或冷却元件,或未深入反应介质足够深度,会导致测量值与实际反应温度存在偏差。例如,在搅拌式反应釜中,传感器若安装在搅拌死角区域,不能真实反映整体物料温度,当搅拌不均匀时,易出现局部温度过高或过低而未被准确检测,导致控温系统误判并触发报警。此外,传感器接线松动、绝缘层破损等安装缺陷会引入电磁干扰,使信号传输过程中产生噪声,造成温度显示波动,引发虚假超差报警。
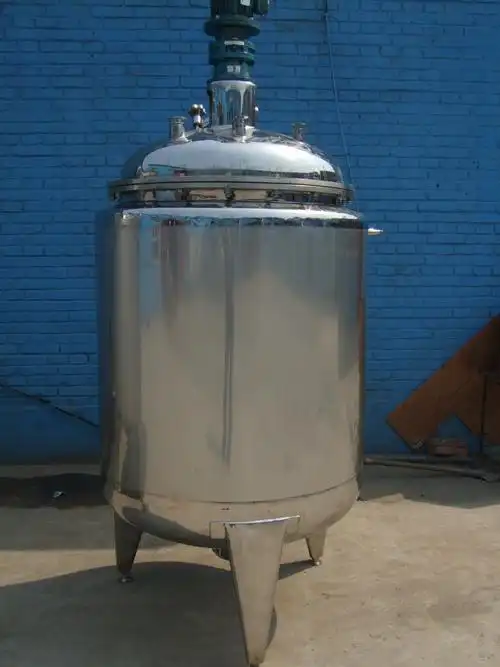
(三)传感器故障与漂移
长期在恶劣环境下运行,传感器可能出现老化、污染、损坏等问题。例如,在含有腐蚀性气体或液体的环境中,传感器探头可能被腐蚀,导致阻值或电势变化异常,测量精度下降。传感器的零点漂移和灵敏度漂移也是常见问题,随着使用时间增长,其输出特性会发生缓慢变化,若未及时校准,会使控温系统的反馈信号与实际温度偏离越来越大,终导致超差报警频繁发生。
二、PID 调节因素分析
PID(比例 - 积分 - 微分)控制是低温反应釜控温系统的核心算法,其参数设置是否合理直接影响控温性能。
(一)比例系数(P)设置不当
比例系数决定了控制器对偏差的响应速度和力度。若比例系数过大,系统会对微小偏差产生强烈反应,导致控制输出波动剧烈,容易引发温度超调,甚至系统振荡,使温度在设定值附近频繁上下波动,超过报警阈值。反之,若比例系数过小,控制器对偏差的纠正作用较弱,温度调节速度缓慢,当系统受到干扰(如进料温度变化、环境温度波动)时,温度恢复到设定值的时间过长,可能因长时间偏离设定值而触发超差报警。
(二)积分时间(I)设置不合理
积分作用的目的是消除静态偏差,使系统在稳态时温度等于设定值。但积分时间过长,积分作用过弱,静态偏差消除缓慢,可能导致温度长时间偏离设定值,尤其是在存在持续干扰(如反应放热或吸热速率变化)时,无法及时调整,引发超差报警。积分时间过短,积分作用过强,会使系统对偏差的累积过快,容易引起控制输出过量,导致温度超调加剧,甚至出现周期性波动,频繁触发报警。
(三)微分时间(D)设置不当
微分作用用于预测温度变化趋势,抑制超调。微分时间过长,会使系统对温度变化的噪声过于敏感,例如传感器信号的微小波动会被放大,导致控制输出频繁变化,反而加剧温度波动,引发不必要的超差报警。微分时间过短,微分作用不明显,无法有效预测温度变化,在温度变化较快的工况下(如快速升温或降温阶段),容易出现较大超调,导致报警频发。
(四)PID 参数未随工况变化调整
低温反应釜的工况可能在反应过程中发生变化,如物料浓度、反应进度、搅拌速度等,这些变化会导致系统的动态特性(如惯性、滞后时间)改变。若 PID 参数是在初始工况下整定的,而未根据实时工况进行自适应调整,当工况变化后,原有的 PID 参数可能不再合适,导致控温性能下降,超差报警频繁出现。
三、解决方案
(一)传感器优化措施
-
合理选型:根据反应釜的工作温度范围、介质特性和精度要求,选择合适的传感器类型和规格。例如,在 - 200℃~50℃范围内,优先选用高精度的铂电阻传感器(如 A 级 Pt100),并确保其耐温、耐腐蚀性满足工况要求。同时,考虑传感器的响应时间,选择能够快速跟随温度变化的型号,如采用薄壁探头结构的传感器。
-
规范安装:传感器应安装在能真实反映反应介质温度的位置,避免靠近加热 / 冷却源和流动死角。在搅拌式反应釜中,建议将传感器安装在搅拌轴附近,深度以探头完全浸入物料且不与搅拌桨碰撞为宜。安装时确保接线牢固,做好绝缘和屏蔽处理,减少电磁干扰。对于高压反应釜,需采用合适的密封安装方式,防止泄漏。
-
定期维护与校准:制定传感器维护计划,定期检查传感器的外观、接线和性能。定期对传感器进行校准,校准周期根据使用频率和工况恶劣程度确定,一般每 3-6 个月校准一次。校准可采用高精度恒温槽作为标准源,将传感器的输出与标准温度值进行对比,若偏差超过允许范围,及时进行调整或更换。
(二)PID 调节优化方法
-
PID 参数整定:采用合适的参数整定方法,如临界比例度法、响应曲线法、Ziegler-Nichols 法等,结合反应釜的实际特性进行 PID 参数初始整定。在整定过程中,逐步调整比例系数、积分时间和微分时间,观察温度响应曲线,以达到的调节效果。理想的响应曲线应具有较小的超调量(一般不超过 5%)、较短的调节时间(根据工艺要求确定)和无明显振荡。
-
自适应调节:对于工况变化较大的反应过程,引入自适应 PID 控制算法,使控制器能够根据实时工况自动调整 PID 参数。例如,利用模糊控制、神经网络等智能算法,实时监测系统的动态特性变化,在线调整比例、积分、微分系数,确保控温系统在不同工况下都能保持良好的性能。
-
分段控制:根据反应过程的不同阶段(如升温阶段、恒温反应阶段、降温阶段),采用不同的 PID 参数。在升温阶段,为加快升温速度,可适当增大比例系数,减小积分时间;在恒温阶段,为提高控温精度,减小比例系数,增大积分时间,同时合理设置微分时间以抑制扰动;在降温阶段,根据降温速率要求,调整 PID 参数以避免超调。
(三)其他辅助措施
-
加强系统抗干扰能力:对传感器信号传输线路进行屏蔽,采用双绞屏蔽线,并将其与动力电缆分开敷设,减少电磁干扰。在控制系统中加入数字滤波算法,对传感器采集的温度信号进行平滑处理,滤除高频噪声,提高信号的稳定性。
-
优化反应釜结构与工艺:确保反应釜的保温性能良好,减少环境温度对反应温度的影响。合理设计搅拌系统,提高物料混合均匀性,避免局部温度差异过大。优化反应工艺,如控制进料温度、流量的稳定性,减少外部干扰对控温系统的影响。
四、结论
低温反应釜控温超差报警频发问题通常是传感器和 PID 调节等多种因素共同作用的结果。通过合理选型、规范安装和定期维护传感器,确保温度信号的准确采集;采用科学的 PID 参数整定和自适应调节方法,使控温系统具有良好的动态和静态性能;同时加强系统抗干扰能力和优化反应釜结构与工艺,能够有效解决超差报警问题,提高低温反应釜的控温精度和稳定性,保障生产过程的安全、高效运行。在实际应用中,应根据具体工况进行详细的分析和调试,必要时结合先进的智能控制技术,实现对低温反应釜控温系统的精准控制。
本文链接地址:http://www.cryoworkes.com/1432.html