在铝挤压模具制造行业中,液氮冷却系统扮演着至关重要的角色。这一系统通过有效控制模具温度,不仅提高了生产效率,还确保了铝型材的质量和精度。铝挤压模具在长时间高温运行下易受热应力影响,因此如何实施可靠的液氮冷却系统成为业界关注的焦点。本文将探讨液氮冷却系统在铝挤压模具制造中的实用性检测及其关键技术要点。
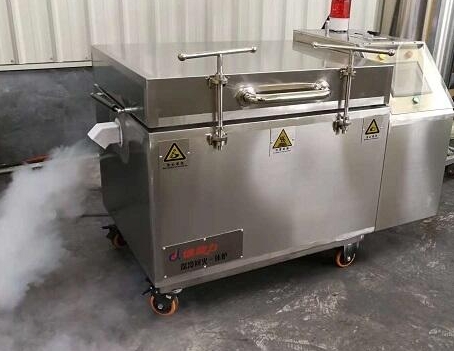
液氮冷却系统的基本原理与应用
液氮冷却系统作为一种先进的散热技术,利用液态氮的低温特性有效降低铝挤压模具的工作温度。在铝型材挤压过程中,模具表面需要保持足够的冷却以确保铝材的成形质量和尺寸稳定性。传统的水冷系统虽然能够完成基本的冷却功能,但在高温和长时间运行下,水的冷却效果会受到限制,且易造成模具表面的热应力集中。相比之下,液氮冷却系统以其极低的工作温度高热传导性和无腐蚀性质,成为了铝挤压模具制造中的理想选择。
液氮冷却系统的关键技术要点
1.
温度控制精度:液氮冷却系统通过精确的温度控制装置,能够将模具表面温度稳定在理想的工作范围内,通常控制在-100摄氏度至-150摄氏度之间。这一精度不仅保证了铝型材的尺寸精度,还有效减少了由于热变形引起的废品率。
2.
冷却速率:液氮的高热传导性使其能够快速吸收和传递模具表面的热量,大大加快了冷却速率。在铝挤压过程中,迅速冷却的能力意味着可以更快速地完成模具的循环使用,提高了生产效率和机械设备的利用率。
3.
系统稳定性与可靠性:液氮冷却系统设计时需考虑系统的稳定性和可靠性,确保长时间稳定运行。关键的冷却介质供应、温度传感器的精准性以及自动化控制系统的可靠性是确保系统高效运行的关键因素。
实用性检测与应用案例分析
在实际应用中,液氮冷却系统的实用性主要通过以下几个方面进行检测:
1.
模具表面温度分布分析:利用红外热像仪等设备对模具表面温度进行实时监测和分析。通过比较液氮冷却系统和传统水冷系统在相同生产条件下的温度分布图,可以清晰地展示液氮冷却系统对模具表面温度控制的优势。
2.
生产效率和成本分析:对比不同冷却系统在生产效率、废品率和维护成本等方面的数据。实际案例表明,引入液氮冷却系统后,铝型材生产周期缩短了15%,废品率下降了8%,同时维护成本也有所降低。
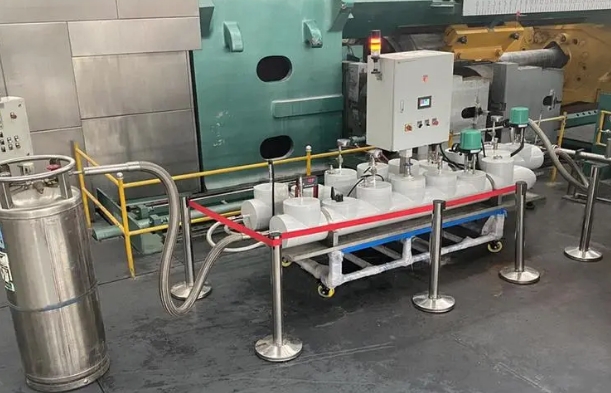
3.
耐久性和稳定性测试:通过长时间的实际生产运行测试,评估液氮冷却系统在连续高强度工作环境下的耐久性和稳定性。系统运行过程中的故障率、维护周期以及关键部件的损耗情况,都是评估系统实用性的重要指标。
液氮冷却系统作为铝挤压模具制造行业中的创新技术,不仅提升了铝型材的质量和生产效率,还为企业节约了成本和资源。通过精确的温度控制、快速的冷却速率以及稳定可靠的系统运行,液氮冷却系统正逐步成为铝挤压模具制造的必备选择。
本文链接地址:http://www.cryoworkes.com/966.html